Technology
Services
EXPERTS IN
COMPOSITE PROCESSING
At Prosix, we are leaders in composite material processing, offering end-to-end solutions that cater to the most demanding applications and environments. Our extensive experience and specialized knowledge in handling composites make us your trusted partner for innovative, high-performance solutions.
EXTENSIVE PROFICIENCY IN
COMPOSITE MANUFACTURING
Services
We provide integrated services across the entire product development lifecycle, including:
- Raw Material Investigation: Research and analysis of primary materials to optimize performance and meet stringent requirements.
- Design and Engineering: Custom design solutions that incorporate FEM analysis, ensuring high precision and efficiency.
- Material Analysis and Modification: Tailoring FRP material properties to enhance performance in specific applications.
- Prototyping and Testing: Fast and reliable prototyping to validate designs, followed by extensive testing to ensure quality and compliance.
- Manufacturing and Process Validation: Defining, testing, and validating manufacturing procedures for consistent, high-quality production.
Qualification for Critical Environments: Expertise in producing components qualified for extreme conditions, including:
- Cryogenic Temperatures
- High Temperatures
- Ultra-High Vacuum
- High Pressure
- High Radiation
- Corrosive Atmospheres
ADVANCED MANUFACTURING APPROACH
Capabilities
Our manufacturing approach is rooted in meticulous design and testing, supported by our capabilities in:
- Part and Mould Design: Precision design to meet exacting standards.
- FRP Material Research: Deep expertise in the development and modification of FRP materials to meet specific application needs.
- Prototype to Series Production: Smooth transition from prototype to pre-series and full-scale production, ensuring consistency at every stage.
- Quality Assurance: Rigorous part validation and comprehensive quality control throughout the production process.
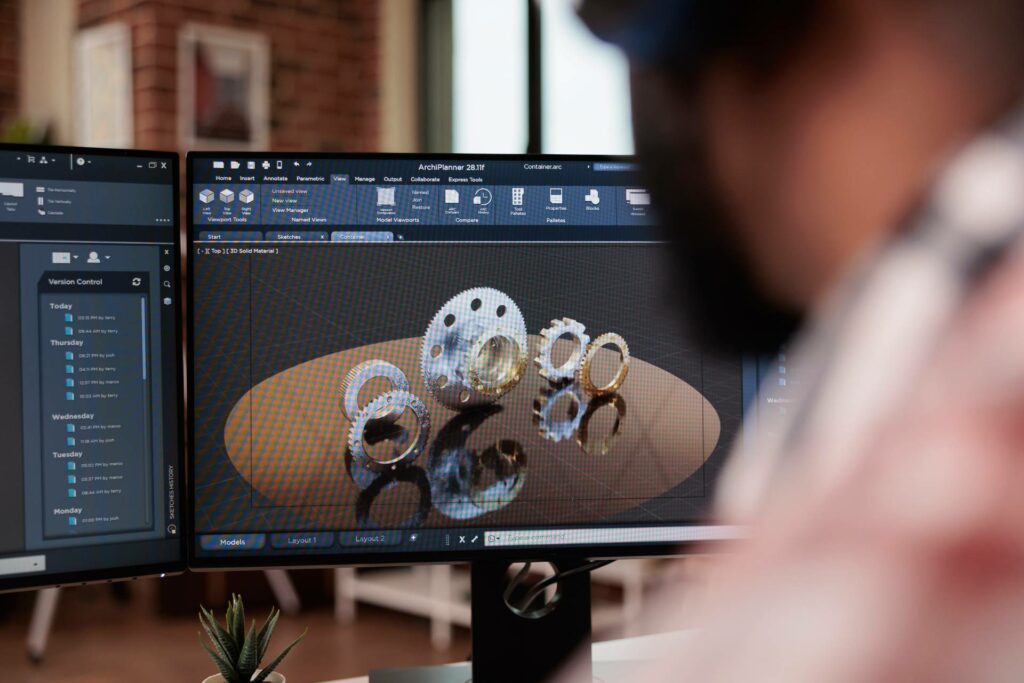
full carbon self deployable booms
COMPOSITES
FABRICATION STRATEGIES
Techniques
Our capabilities cover a wide range of composite manufacturing techniques, including:
- Closed Molding Processes (Infusion, Press)
Closed molding uses sealed molds for processes like vacuum infusion and press molding, ensuring precise resin flow and high-quality surface finishes. Ideal for complex shapes and high-volume production, it provides consistent, strong parts with minimal waste. - Resin Transfer Molding (RTM)
RTM injects resin into a mold containing dry fibers, offering control over fiber alignment and part thickness. It’s suited for large, complex parts with consistent quality, often used in aerospace and automotive sectors. - Prepreg Layup
Prepreg layup uses pre-impregnated fiber sheets that are precisely laid and cured, typically in an autoclave. This method is favored for high-performance applications requiring lightweight and high-strength components, such as in aerospace. - Autoclave and Out-of-Autoclave Processes
Autoclave curing applies heat and pressure for optimal composite strength, while out-of-autoclave (OOA) methods, like vacuum bagging, offer a cost-effective alternative for large parts without needing expensive autoclaves. - Monolithic and Sandwich Structures
Monolithic structures are single-layer composites offering strength with simplicity. Sandwich structures combine a lightweight core with composite skins for exceptional stiffness-to-weight ratios, commonly used in aerospace and marine industries. - All Core Types
Core materials vary by need: foam for versatility, honeycomb for high strength-to-weight, and balsa for stiffness. Each is chosen based on specific application demands like impact resistance or weight reduction.
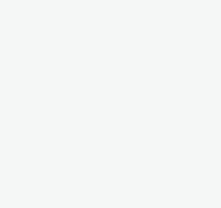
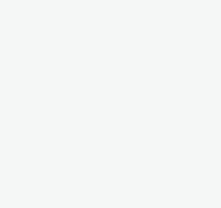
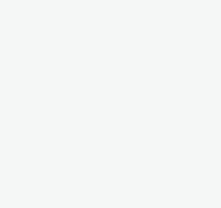
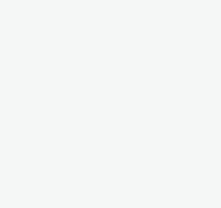
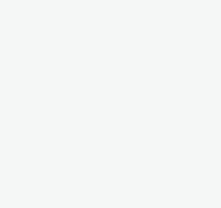
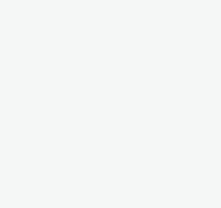
Our expertise allows us to deliver tailored solutions that meet the unique demands of every project, regardless of complexity. Each of the manufacturing methods we employ is recommended based on specific requirements, such as the geometric complexity and dimensions of the piece, the desired physical properties, and the final visual appearance. Additionally, the type of materials, production output, and cost considerations are critical factors in determining the best approach. By carefully evaluating these parameters, we ensure that the optimal composite processing technique is chosen to achieve superior performance, efficiency, and cost-effectiveness, no matter the complexity or scale of your project.